자동차, 선박, 항공기 등 중공업 제품을 비롯하여 세상의 많은 사물이 합금으로 제작되고 있다. 그러나 친환경성의 중요성이 높아지면서 세계의 재료 연구자들은 더 개선된 성능의 신소재를 개발하기 위해 끊임없이 연구해왔다.
합금을 대체할 신소재로 많은 연구자들의 관심을 받은 후보는, 금속보다 내열 온도가 높고 훨씬 가벼운 세라믹이다. 하지만 세라믹 활용을 극대화하기 위해서는, 깨지기 쉬운 세라믹의 숙명적 특성을 극복해야 한다. 이는 절대 쉬운 과제가 아니다.
항공기 엔진 분야는 고열의 환경을 견디는 동시에 경량화가 요구되는 세라믹 소재 활용을 수십 년간 기대해왔다. 하지만, 지난 2001년 미국 국방연구원 (Institute of Defense Analyses)에서 “세라믹보다 돼지가 먼저 하늘을 날 것인가? (Will Pigs Fly Before Ceramics do?)”라는 보고서를 발행할 정도로 세라믹을 항공기 엔진 분야에 적용하는 데 어려움은 매우 컸다.
GE는 20년에 걸친 연구 끝에, 2015년 CMC 즉 세라믹 매트릭스 복합소재 부품을 채용한 차세대 항공기 엔진인 LEAP의 시험 비행에 성공했다. CMC 소재로 만든 부품은 밀도가 합금의 1/3 수준으로 가볍고, 합금보다 열팽창이나 변형이 적어 항공기 엔진 설계에 새로운 장을 열었다.
팬 블레이드가 경량화되면, 원심력이 줄고 베어링 및 기타 부품도 더욱 슬림하게 만들 수 있어 연료 소모나 환경에도 큰 영향을 미친다. 뛰어난 내열성 덕분에 공기 냉각이 불필요해져 연료 소비도 대폭 줄어드는 등 혁명적인 혜택을 가져온 신소재 CMC는 향후 세계 최대 제트엔진인 GE9X에도 사용될 예정이다.
CMC란 무엇인가
CMC는 탄화규소 매트릭스(기지) 내부에 특수한 탄화규소 세라믹 섬유가 고정된 구조로, 열 차폐 코팅으로 마무리한다. 머리카락보다 가느다란 탄화규소 섬유 하나 하나를 세라믹으로 코팅하고, 이 섬유들을 격자 모양으로 틀을 잡은 세라믹 수지에 담근 후, 모든 세라믹이 겪게 되는 숙명에 따라 오븐에 구우면 된다. 그 결과 세라믹 섬유는 다공(多孔)의 격자 구조로 변환된다. 격자 위에 실리콘을 녹이면 실리콘은 격자 구조 사이 사이에 스며든다. 즉 섬유를 세라믹 코팅하는 것이 CMC제조의 비법인 것이다. 이렇게 소재를 얻으면 다이아몬드 그라인더를 이용, 원하는 형태로 가공하면 된다. GE글로벌리서치 연구진과 GE의 여러 사업 분야에서 상업적으로 활용될 수 있는 CMC를 개발해왔다.
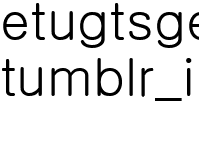
30년 이상을 이어져온 연구
깨지기 쉬운 세라믹이 합금을 뛰어넘는 강한 소재로 변모할 수 있었던 것은 니폰카본(日本カーボン)이 개발한 탄화규소연속섬유 하이니칼론(Hi-Nicalon) 덕분이다. 내열 합금보다 강도가 높으면서도 가벼운 이 섬유를 세라믹과 섞어 소성(燒成)하여 세라믹의 약점을 해결한 것이다.

이치카와 히로시(市川宏)는 니폰카본 연구진 중 한 사람으로, 과거 연구소장을 역임했다. 그는 현재 은퇴했지만, 일본의 소재 개발 기업을 계속 지원하고 있다. “이야, 드디어 꿈이 이루어졌습니다. ‘드디어 우리의 생활을 바꾸는 소재를 만들었구나’라고 생각합니다.” 말하는 그의 눈가엔 주름이 잡힌다.
탄화규소섬유 자체는 도호쿠(東北) 대학 금속재료연구소의 고(故) 야지마(矢島) 교수 연구진이 약 40년 전 1975년에 발명한 것이다. 금속, 수지, 플라스틱 등의 강화용 섬유로 매우 유망했던 이 소재를 ‘꿈의 섬유’로 판단한 니폰카본은 바로 제조권을 취득했다. 이때 양산화 프로젝트의 리더로 임명된 사람이 당시 34세였던 이치카와 씨였다.
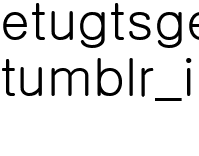
이치카와 히로시(市川 宏)
미국 세라믹 협회 회원 / 전 니폰카본 연구소 소장 (사진: GE일본)
“본격적인 생산을 준비하기 위해 도호쿠 대학 연구실에서 몇 개월을 보냈습니다. 처음 제조법을 봤을 때 그 기상천외함에 너무나 놀랐습니다.” 이치카와 씨의 회상이다. “폴리카르보실란(Polycarbosilane)이라는 고분자물질을 벤젠에 녹인 후 용기에서 졸인 다음, 유리 막대를 깊숙이 넣어 끈끈한 실처럼 늘어지는 시점을 확인한 뒤, 그 유리 막대를 들고 부웅 달려서 실처럼 늘어트리는… 장면이었습니다. 게다가 이 물질은 섬유라고 해도 보통 실과 달리 설탕 공예처럼 약했죠. 손으로 만지려 하면 가루로 부서져 버렸습니다.”
화학 전문가 이치카와 씨와 개발팀은 고분자 물질을 녹여 섬유를 만드는 것에 관한 지식이 없었다. 그들은 뽑아낸 실을 쪄 내기도 하고, 태워보기도 했다. 찌는 과정에서 섬유가 녹지 않게 새로운 가공 기술도 필요해졌다. 연구원들은 관련 분야 권위자를 찾아 다니며 전공을 넘어선 지식이나 도움도 받았다. 마침내 개발팀은 샬레와 유리 막대기로는 열심히 달려도 2~3m 길이 밖에 만들 수 없었던 탄화규소 섬유를, 불과 3년만에 1,000m의 연속섬유로 방사하는 제조기술을 만들어냈다.
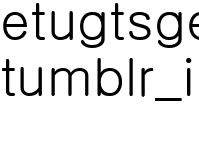
NGS 어드밴스트 파이버, 도야마 공장 (촬영: GE일본)
1983년에는 월간 1톤의 생산 능력을 지닌 공장이 준공되었다. 제품명을 ‘니카론’으로 정하고 상업 생산을 개시했지만, 시장 반응이 거의 없어앞으로 활약할 날만 기다리는 장기전이 시작됐다. 우주선이 지구로 귀환할 때 발생하는 마찰열을 견디기 위한 타일의 이음새 보강에 사용되는 등 니카론 소재의 특성이 빛난 응용 사례도 있었지만, 이치카와 씨가 근무할 당시 충분한 수익을 얻을 정도로 발전한 일은 없었다고 한다. 그는 이 시간을 이렇게 회고한다.
“첫 생산분부터 재고가 되었죠. 엄청나게 부담이 됐습니다. 하지만 최초로 양산했다는 사실이 좋았어요. 전세계에 샘플을 뿌리고, ‘사용 가능성을 봐주세요’라는 요청과 함께 응용 가능성을 찾았으니까요.”
세계의 과학자 기술자와 함께 완성하다
“탄화규소 섬유가 완성될 수 있었던 것은 CMC 개발에 참여한 전세계 과학자들 덕분입니다.” 이치카와 전 소장의 말이다. 니폰카본의 개발팀은 전세계 과학자로부터 피드백을 받으며 규소(Si)와 탄소(C)를 베이스로 하는 소재를 지속적으로 개량했다. 니칼론(SiCO)→하이니칼론(Si-C)→하이니칼론 타입S(SiC)로 진화한 것이다.
니칼론(SiCO)은 1,200도 이상에서 산소가 분해돼 성능이 떨어지는 문제점이 있어, 산소를 없앤 Si-C로 해결하려 했다. 하지만 Si-C는 1,000도 이상에서 섬유가 늘어나 변형하는(크리프 현상) 약점이 있어, 규소와 탄소의 비율을 1:1에 가깝게 결정 성장(crystal Growth)시킨 탄화규소(SiC)를 개발했다. 이 SiC (하이니칼론 타입S)가 GE의 CMC 기술을 완성하는 꿈의 섬유이다. 이 개발은 이치카와 연구팀의 일원이었던 다케다 미치오(武田道夫) 씨가 담당했다.
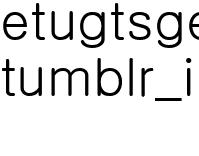
“미스터 SiC”라 불리는 다케다 미치오, NGS 어드밴스트 파이버 주식회사 사장 (사진: GE일본)
개발 과정을 통해 ‘미스터 SiC’라는 별명을 얻은 다케다 미치오 NGS 어드밴스트 파이버 사장은 이렇게 말한다. “탄소과 규소의 비율을 1:1이라는 극한까지 내렸지만, 1,000도를 넘으면 산화가 시작되는 것을 피할 수 없습니다. 섬유를 단독으로 사용하지 않고 세라믹과 함께 사용하여 CMC를 만든 것은 탄화규소 섬유에 있어 운명적 만남이었습니다. 30대 시절, 한밤중까지 연구에 열중해 현미경을 보다가 “큰일 났네, 막차 시간이다!”라며 당황해 연구소를 나오는 일도 자주 있었죠. 그래도 연구를 하면서 즐거웠습니다. 세상 어디에도 없는 물질을 취급할 수 있는 것도 기뻤습니다.”
당시에도 CMC 개발은 세계적으로 많은 관심을 받고 있었고, 업계에서도 매년 약 50편의 관련 논문이 발표되었다. 다케다 마치오 씨도 매년 1월 미국 플로리다에서 개최되는 세라믹학회 연례 회의에서 매년 연구 성과를 발표하며, CMC 상용화를 위한 전세계의 움직임에 동참했다. 당시 상사였던 이치카와 히로시 씨는 “이 회의는 항상 정초 직후에 일정이 잡혀 있어서, 다케다 마치오 씨는 연말도 연초도 매년 회사에서 발표를 준비하고 있었습니다.”라고 이야기한다.
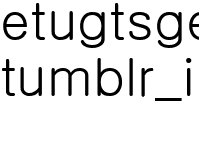
연구소 시절의 다케다 마치오, 섬유 500개를 종이에 붙여 현미경으로 그 두께를 측정하는 작업을 진행했다. (사진: 니폰카본)
당시 ‘미국에는 없고 세계에 있는 기술 20’에 포함됐던 탄화규소 섬유였으나, 대규모의 수요는 여전히 없었다. 니칼론의 품질 수준을 넘지 못한 많은 기업들이 철수했기에, 현재 탄화규소 섬유를 제조할 수 있는 기업은 전세계에 단 두 곳뿐이다.
원래 몇 년간의 단기 연구만으로는 성과가 나지 않는 것이 재료 분야 연구 개발의 특징이다. 탄생부터 현재까지 약 40여 년이란 긴 세월 동안 니폰카본이 개발을 지속할 수 있었던 배경에는, 신소재의 가능성이 가진 가치를 세계에 전달해야 한다는 책임감이 있었다고 한다. 오랫동안 CMC를 연구한 끝에 GE가 세라믹으로 하늘을 나는 꿈을 실현할 수 있었던 것은 니폰카본의 투자 덕분이며, 모든 연구 개발자들의 노력해온 결과다.
GE가 CMC 제조를 본격화하면서, 니폰카본은 탄화규소 섬유의 양산을 위해 GE 및 프랑스 사프란과 함께 합작사인 NGS 어드밴스트 파이버 주식회사를 설립했다. (니폰카본 50%, GE 및 사프란 각 25% 출자) 탄화규소 섬유는 현재 도야마 현에서 생산 중이며, 추가 공장을 증설 하고 있다. 2016년에 가동을 시작하는 신공장에서는 탄화규소 섬유를 본격적으로 양산해 미국의 GE 공장으로 출하할 예정이다.
미국 내에서도 탄화규소 섬유 생산을 목적으로한 공장 건설이 진행 중이다. 미스터 SiC 다케다 마치오 사장은 지난 2015년 봄 NGS 어드밴스트 파이버 사장으로 취임하여 일본과 미국에서 탄화규소 섬유의 본격 양산을 진행하고 있다.
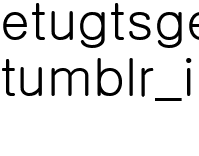
건설 중인 NGS 어드뱐스트 파이버 신공장은 2016년에 가동을 시작해 연간 10톤을 생산할 예정이다. (사진: GE일본)
CMC 기술은 향후 발전용 가스 터빈 등 다양한 분야에서 응용되어 앞으로 첨단 산업 분야의 효율성 향상에 크게 기여할 것이다.